Chassis – arm – electronic integration (V)
While the Spanish team worked on the entire electronic and software system, the French team with the industrial designer David Pugnet worked on the sensor arm bracket.
Below is an advanced design of it.
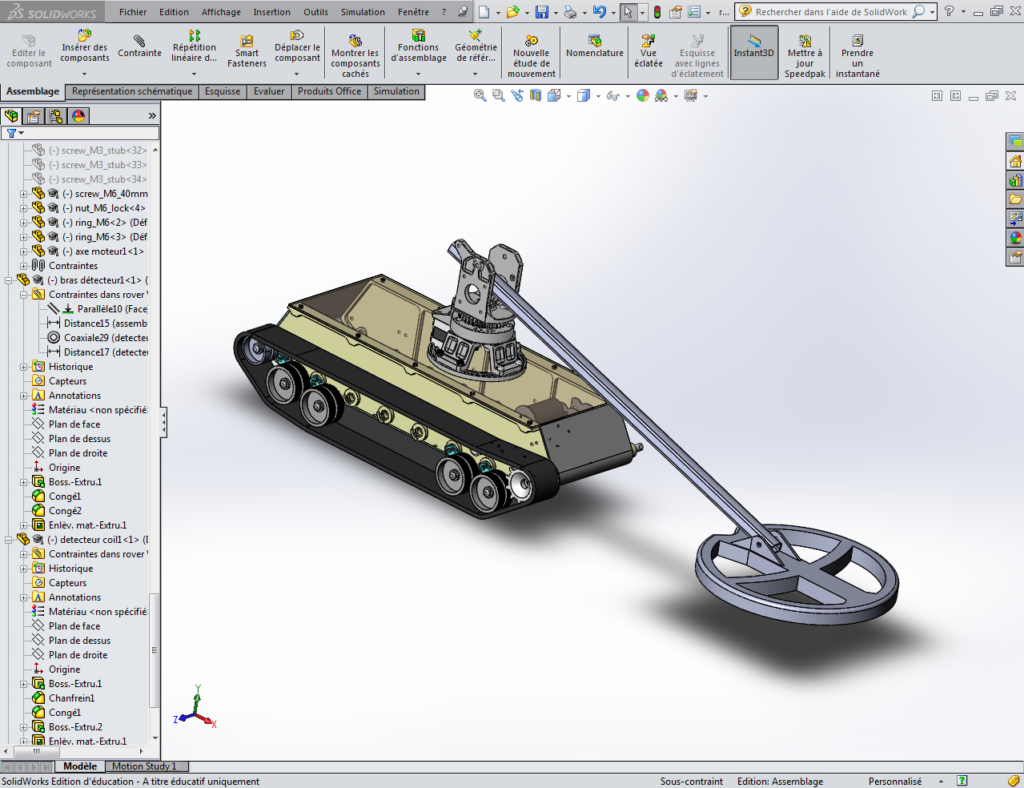
Although we have relied on Florin Tobler’s design for certain parts, some such as the parts that grip the sensor arm have been designed under David’s expertise.
Below is also the detail of the system that connects arm and sensor:
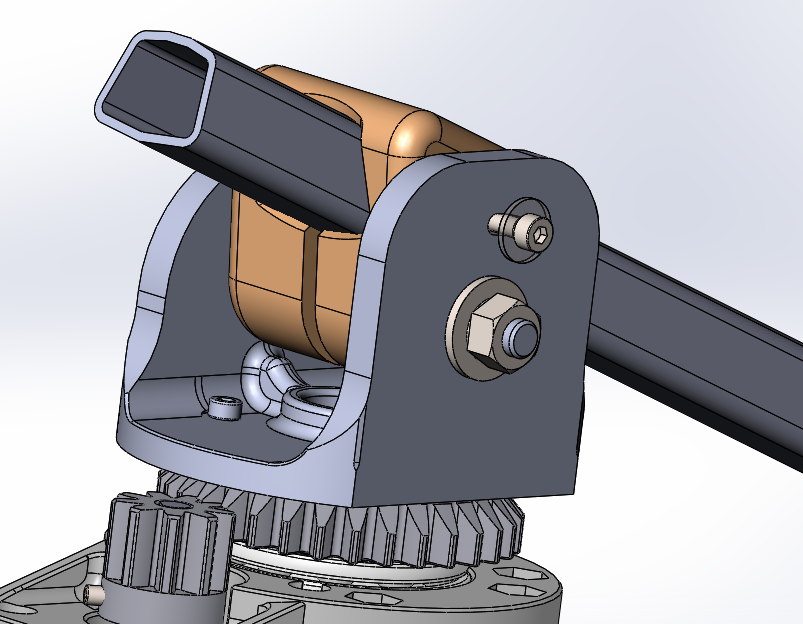
We had a discussion about whether to add a counterweight or not. David’s solution has a screw to adjust the sensor arm and does not appear to require a counterweight. However, like many other parts of the project, we are going to test whether it is necessary to carry it out or not. Testing the solutions with the students is one of the most enriching activities since solutions can be proposed to the possible problems that arise.
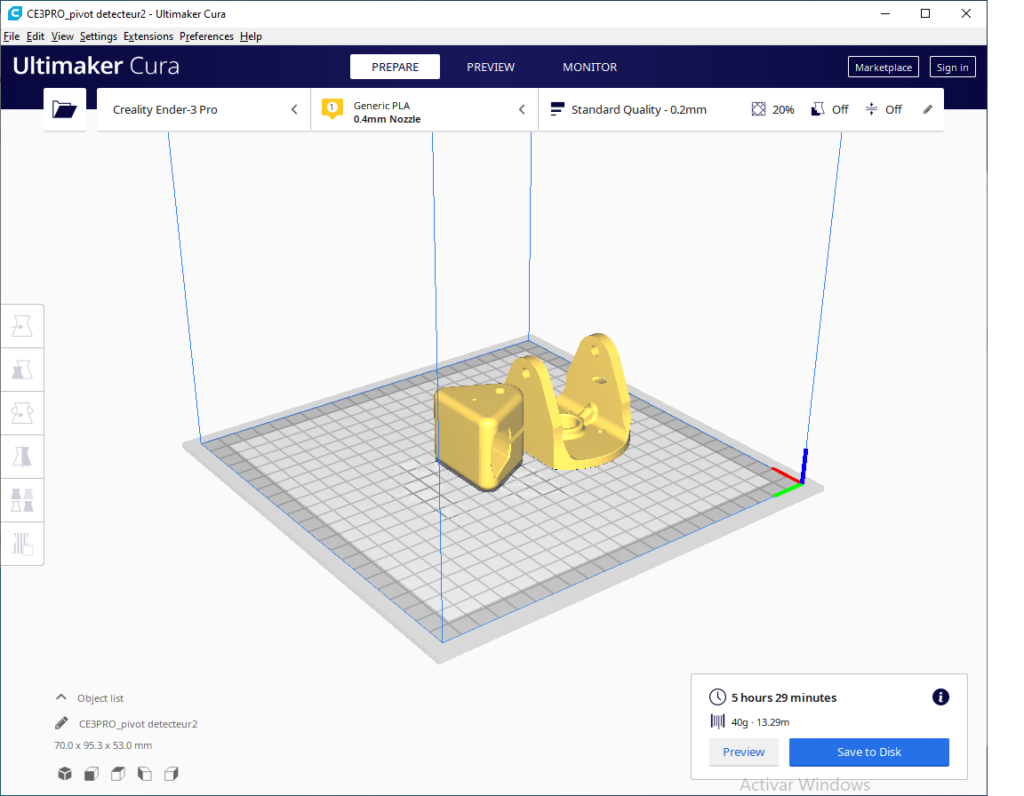
Once the French designs were received, the Spanish team got down to business printing the parts received.
The pieces are going to be printed in PLA with a density of 90% -100% so that they provide the necessary strength and can resist bending and friction.
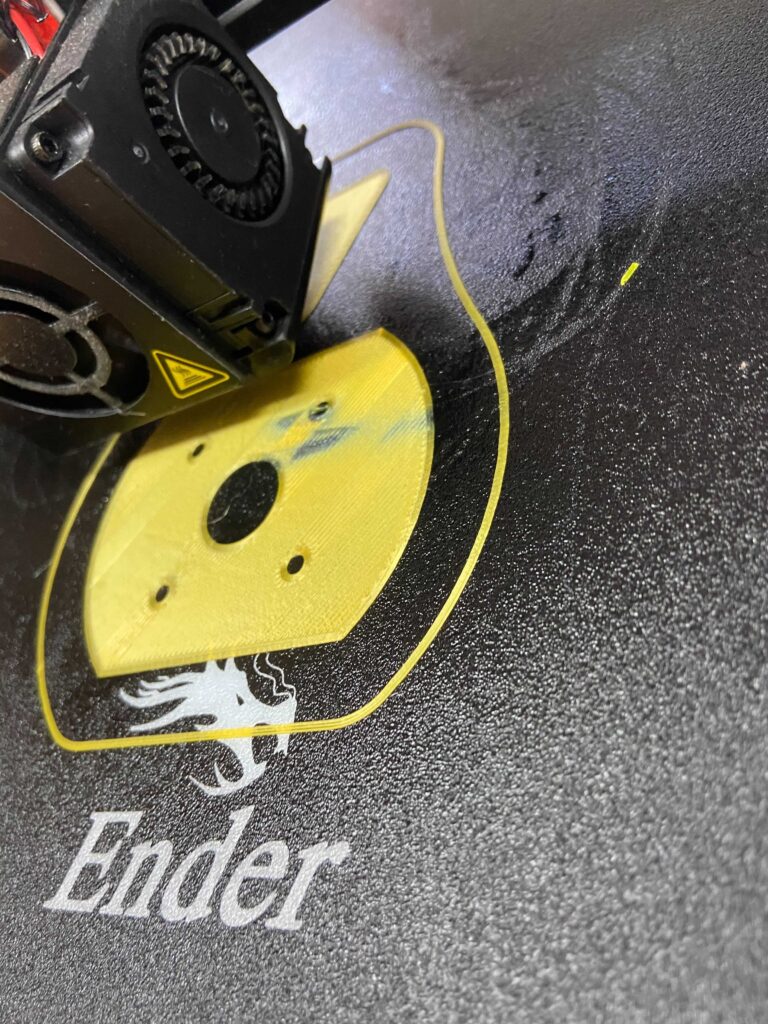
The French team for its part decided to print the pieces in ABS with a density of 50%. ABS is a more resistant plastic and suitable for mechanical parts but the problem it presents is its shrinkage which makes it difficult to print.
In the following image you can see the result of the ABS printing by François, the master of 3Dprint in the french team.
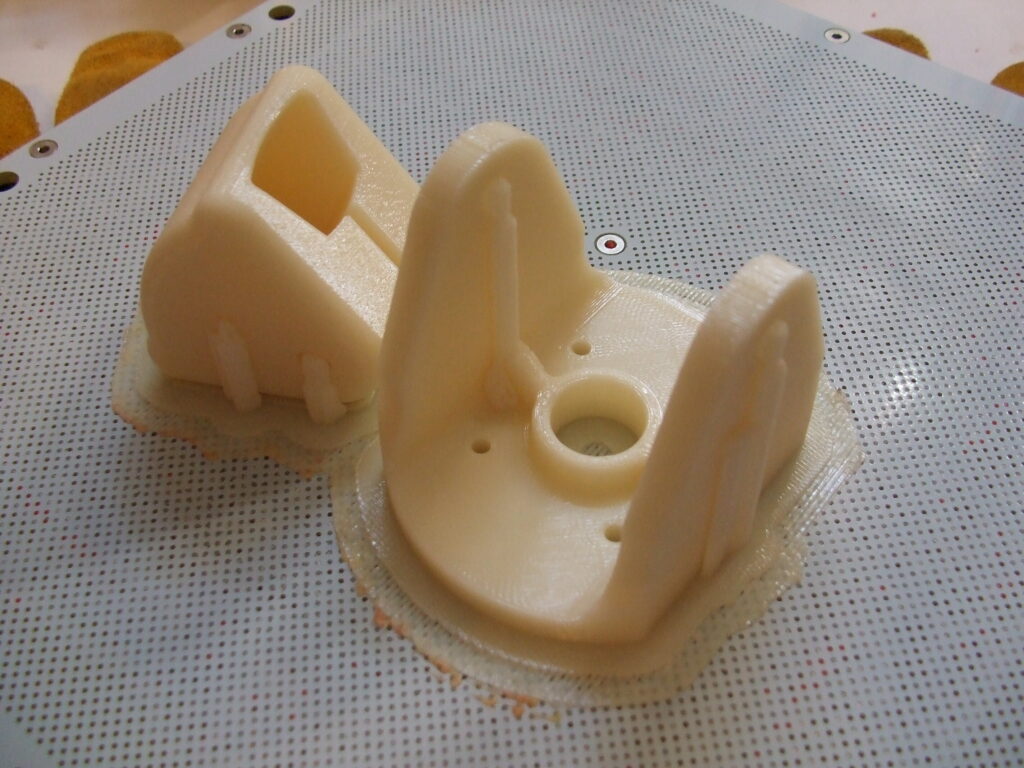